مکنده کاتالیست (کاتالیزور سیال بستر) فرآیند تبدیل به شمار می رود که در آن مواد سنگین و بی ارزش نفتی به مواد سبک و ارزشمند مبدل می شود و به عنوان افزایش دهنده سرعت در فرآیند های شیمیایی و سرعت و شرایط بهینه حائز و اهمیت می باشد و مورد استفاده قرار می گیرد. در دنیای امروز با افزایش بی رویه مصرف سوخت نیازمندی به این سیستم بیش از پیش ارزشمند شده زیرا تبدیل مواد سنگین به سوخت های سبک امری اساسی تلقی میشود و رواج تکنولوژی کاتالیست در جهت شکست مولکول های نفتی در همه پالایشگاه های دنیا مورد استفاده قرار می گیرد که در طی این فرآیند شگفت انگیز برس های سنگین به محصولی سبک به نام کک تبدیل می شود، از کاتالیست ها در صنعت نفت، گاز و پتروشیمی استفاده می گردد. کاتالیست در صنعت نفت و گاز در دو فرایند کراکینگ (شکستن و تجزیه مولکول های درشت به مولکول های کوچک تر) و رفرمینگ (بازآرایی مجدد و ترکیب مولکول ها برای تولید) استفاده می شود. در صنایع پتروشیمی نسبت به صنعت نفت و گاز فرآیند های کاتالیزوری حجم کمتری را اشغال می کند اما محصولات تولید شده آن بسیار مهم تر و متنوع تر هستند که گاهی اوقات نیاز است تا برای تخلیه و یا انتقال این مواد شیمیایی (کاتالیزور ها) از یک سیستم تخلیه پنوماتیک استفاده شود. مکنده کاتالیست نوعی سیستم دارد که به خوبی می تواند بدون آسیب به مواد شکننده، آن ها را از راکتور تخلیه جابجا کند. مکانیزم عمل این دستگاه به این صورت است که به هنگام استفاده دهانه مخروطی کاملا عمودی شده و مطابق با مکنده های صنعتی دیگر، فرآیند مکش به منظور جابجایی و یا تخلیه کاتالیست هرا به انجام برساند. بهره گیری از این سرشاز از مزیت های گوناگونی است که به رشد صنایع نفت، گاز و پتروشیمی کمک شایانی خواهد کرد.
در سال های اخیر فناوری ساخت و به کارگیری کاتالیست بیش از گذشته مورد توجه واقع شده و تحقیقات گسترده ای در بکارگیری آن به انجام رسیده. کاتالیست حتی میتواند در ابعاد نانو تولید شده و به کمک بخار آب حاوی آمونیاک در دمای بالا ترکیب و با اکسیدهای فلزات قلیایی کمیاب فعال گردد که از آن میتوان جهت کاهش الفین در فرایند FCC و برای بالا بردن عدد اکتان بنزین بهره مند شد. اکسید گالیم به همراه کاتالیست بر روی فعالیت و میزان پایداری نانوکاتالیست تاثیرگذار است، به طوری که میزان مناسبی از این اکسید سبب افزایش کارایی آن شده و در پایداری آن ماثر است.
کاتالیزور ذراتی با اندازههای مختلف میباشد و از ۱۰–۰ یا۲۰–۱۰ میکرون آغاز شده و تا بزرگترین ذرات در حدود ۸۰ میکرون به بالا میباشد. اندازه مطلوب و ایدهآل آن به میزان تقریبی ۸۰–۲۰ میکرون تخمین زده شده،ذرات ریز کاتالیز باعث افزایش مصرف کاتالیست از دودکش گازهای سوخته و مواد نفتی خارج شده می گردد و میزان بازیافت سیستم کاتالیست را افزایش می دهد حالا اگر ذرات کاتالیست در سیستم درشت باشد روانی در مخلوط جامد و گاز وجود نخواهد داشت و از طرفی چگالی افزایش می یابد، عدم یکنواختی در جامد و گاز بودن موجب می شود که عملیات به درستی صورت نپذیرد و منجر به تولید کربن شود.
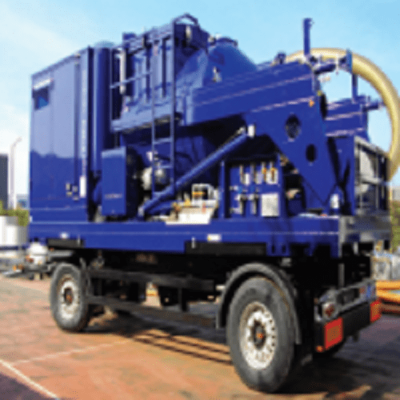
فرآیند کاتالیسیت
در روند انجام عملیات، کاتالیست به برش های سنگین و سبک و کک تبدیل شده و کک بر سطح کاتالیست رسوب می کند و در قسمت احیا سوزانده میشود و انرژی مورد نیاز فرایند را تأمین میکند. در این میان به غیر از بنزین محصولات دیگری همچون گازهای متان و اتان و ترکیباتی به سنگینی ماده اولیه پدید میآید و تولید آن ها بستگی مستقیم به شرایط عملیاتی خواهد داشت.
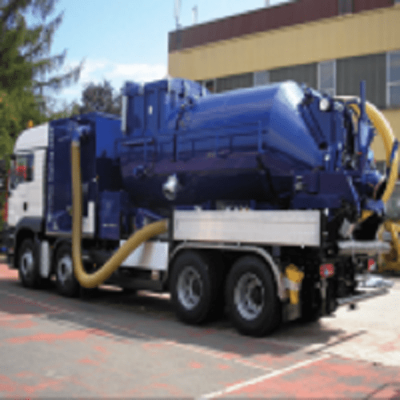
مزایای استفاده از دستگاه مکنده کاتالیست
بهره گیری از مکنده کاتالیست به منظور جابجایی و یا تخلیه این مواد از راکتور ها، تنها راه ممکن نیست اما بهترین راه می باشد. این دستگاه به مانند دیگر دستگاه های نظافت صنعتی فعالیت مورد نیاز خود را در بهینه ترین حالت ممکن به انجام می رساند و مزایای بسیاری به همراه خواهد داشت. قابلیت فعالیت مکنده در یک سیکل بسته نیتروژن به منظور جلوگیری از مجاورت کاتالیست ها با اکسیژن موجود در هوا و بروز فرآیند های شیمیایی مضر صورت می گیرد، مجهز بودن به سیستم خنک کننده گاز نیتروژن در هنگام خروج از پمپ و بازیابی گاز ارزشمند و گران قیمت نیتروژن به راکتور های حاوی کاتالیست، راندمان بالای سیستم فیلتراسیون دستگاه، قابلیت مکش بیش از ۱۰ تن کاتالیست در هر ساعت را به دنبال دارد، استفاده از این مکنده، امکان تغییر قدرت دستگاه به درخواست مشتری و بسته به نیاز از ۴۲ تا ۲۳۰ کیلو وات، تخلیه سریع و بی خطر کاتالیست ها از راکتور، امکان پر کردن راکتور ها (انتقال کاتالیست ها به بالای راکتور) با استفاده از این دستگاه کاربردی، امکان جداسازی نرمه و خاک از کاتالیست ها به وسیله مکنده کاتالیست صنعتی در حین انجام عملیات انتقال کاتالیزور و انتقال کاتالیست ها به مخزن جداگانه و در نهایت عدم آسیب به این مواد مهم شکننده و کاربردی در صنایع گوناگون همگی از مزایای استفاده از دستگاه مکش کاتالیست هستند،نیز مهم ترین ویژگی این دستگاه مکنده صنعتی حائز اهمیت بودن این مسئله است که برخی کاتالیزور ها می بایست با تجهیز به سیستم های مخصوص در محیط نیتروژنی (ازت) تخلیه گردند؛ که به سادگی و در بهینه ترین حالت ممکن این امکان را داده و پس از انجام عملیات انتقال، نیتروژن به داخل راکتور منتقل شود.
دستگاه مکنده کاتالیست وسیله ای مناسب و ویژه برای استفاده در صنایع نفت، گاز و پتروشیمی می باشد، زمان بهره مندی از این ابزار کاربردی درست در هنگام تعمیرات اساسی خواهد بود که نیاز به یک سیستم انتقال مواد پنوماتیک احساس می شود و برای تخلیه کاتالیست و شارژ مجدد سرامیک بال مکنده مناسب به شمار می رود.
مکنده کاتالیست برای تخلیه راکتورها و مطابق با خواسته کاربر طراحی و تشکیل و ساخته شده و بارگیری راکتورها گزینه مناسبی برای ان محسوب می شود.
تخلیه سریع
تخلیه با کاتالیست در مدت زمان بسیار کمی در مقایسه با روش های سنتی و قدیمی به انجام می رسد و سرعت قابل توجه در این کار هزینه تعمیرات دستگاه را به شکلی کاملا محسوس کاهش می دهد و با وجود راکتور گازهای خطرناک و بی خطر، بدون نیاز به کاربر تخلیه می شود.
امکان پر کردن راکتور
دستگاه مکنده تخلیه کاتالیست برای انتقال در قسمت بالای راکتور قرار گرفته و با نصب مخزن دستگاه بر ورودی مکش کاتالیست از بشکه ها در زیر راکتور صورت داده و بر بالای راکتور انتقال می دهد.
امکان تخلیه در محیط نیتروژن (ازت)
در صورت امکان با تعبیه سیستمی مخصوص می توان کاتالیست را در محیط ازت تخلیه و مجدداً گاز به داخل آن هدایت کرد و از تماس کاتالیست با اکسیژن ممانعت نمود.
امکان جدا سازی در کاتالیست
کاتالیست مکیده توسط دستگاه از نرمه و خاک جدا شده و در مخزن به صورت جداگانه جمع آوری می گردد.